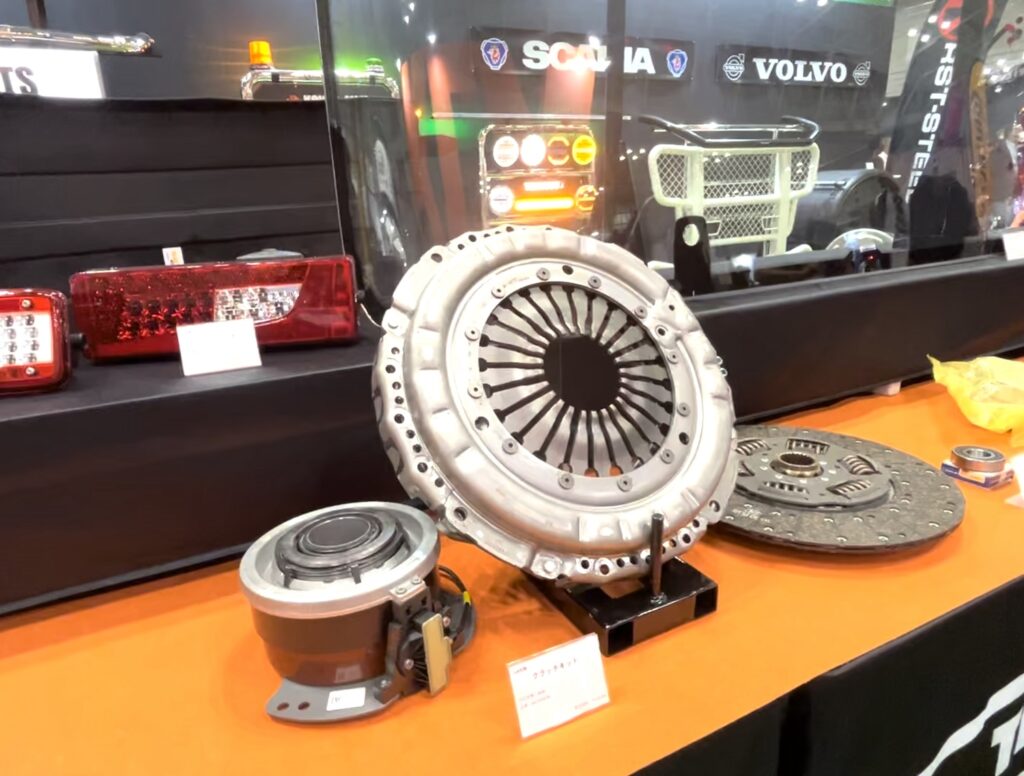
最近はAMT(自動変速MT)やATのトラックも増えてきたが、乗用車と比べればMT比率はまだまだ高い。MTの場合、変速機の寿命や燃費を左右するのがドライバーのクラッチ操作だ。
クラッチの寿命自体、ドライバーの操作で大きく左右される。乗用車でもポルシェ911はMTの保護のためにクラッチを弱く作ってある、なんて噂も出回るくらいクラッチの寿命は短めで、下手なオーナーはメンテナンス費用が嵩むらしい。
トラックのクラッチの耐久性は乗用車より高いけれど、それはトラックというクルマの特性を考えれば当然のことだ。使用目的や環境にもよるが、年間の走行距離では乗用車よりトラックの方が格段にたくさんの距離を走る。
車検が毎年あるとしても、クラッチの交換頻度が高ければ整備にかかる時間や費用も嵩んでしまうから、トラック事業者はそんなメーカーのトラックを使わなくなる。トラックは丈夫でメンテナンス頻度も少なく、短時間でメンテナンスが終わる方が稼働時間が長く取れるからだ。
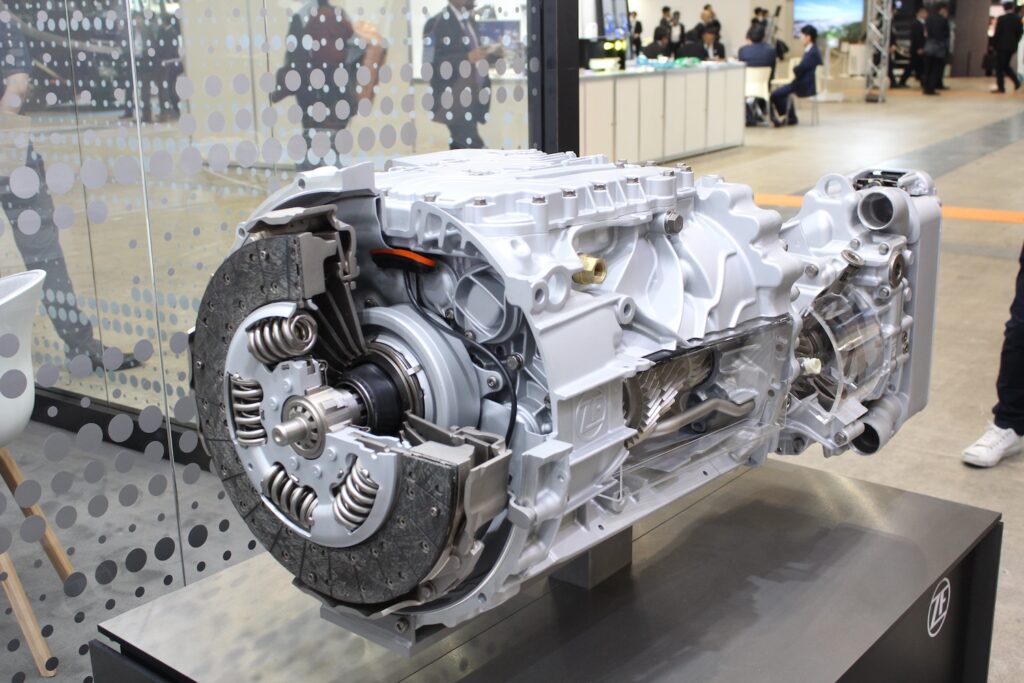
トラックドライバーは一般のドライバーよりもクルマを運転する頻度も高く、プロ意識もあるので運転は上手な傾向にある。しかし荷物を積んで、勾配のあるところなどを走る機会が多ければ、クラッチの負担は増すので、クラッチの寿命は短くなりメンテナンス頻度は高くなる。
そのため大手のトラック事業者の中には、大型トラック20万km無交換は運転技術の高さの証として会社から表彰されることもある。それくらい、クラッチの寿命はトラックドライバーの運転の仕方で変わってくるのだ。
しかし、それならクラッチの摩擦材を分厚くして、100万kmくらい走れる仕様にしてもいいのでは、と思うかもしれない。確かに摩耗していくクラッチ板の厚さを増やせば耐久性は高まるように思える。
けれども、そんなクラッチ強化策はいくつかの理由で実現が不可能、あるいは不十分なのだ。それをこれから説明しよう。
まずクラッチ板の摩擦材は摩擦によって動力を伝えるため、圧縮して固めてあるが、それほど強度的に強いものではないから厚みには限度がある。あまりに厚くしてしまうと、クラッチカバーの圧着力や発進時などの衝撃で割れてしまうこともあり得る。
乗用車の世界では競技用の強化クラッチには、摩擦材に金属の粉末を焼結したメタル材を使うこともある。こちらは強度面や耐久性は高いが、フライホイールへの攻撃性が高く、高負荷な走行が多いトラックには向いていない。
またクラッチが繋がる時の衝撃を和らげるため、クラッチ板にはダンパースプリングが備わっている。これは発進時や変速時に衝撃を受け止めるので、経年劣化により折れてしまうことも珍しくない。
クラッチ板の摩擦材が擦り切れる前にダンパースプリングが折れてしまうと、結局メンテナンスの必要性が生じるのだ。
クラッチカバーを押してクラッチを断続させるレリーズベアリングにも寿命がある。さらには摺動部の潤滑やクラッチ部分の点検の必要性もあって、ある程度定期的なメンテナンスが必要となるのがクラッチ系なのである。
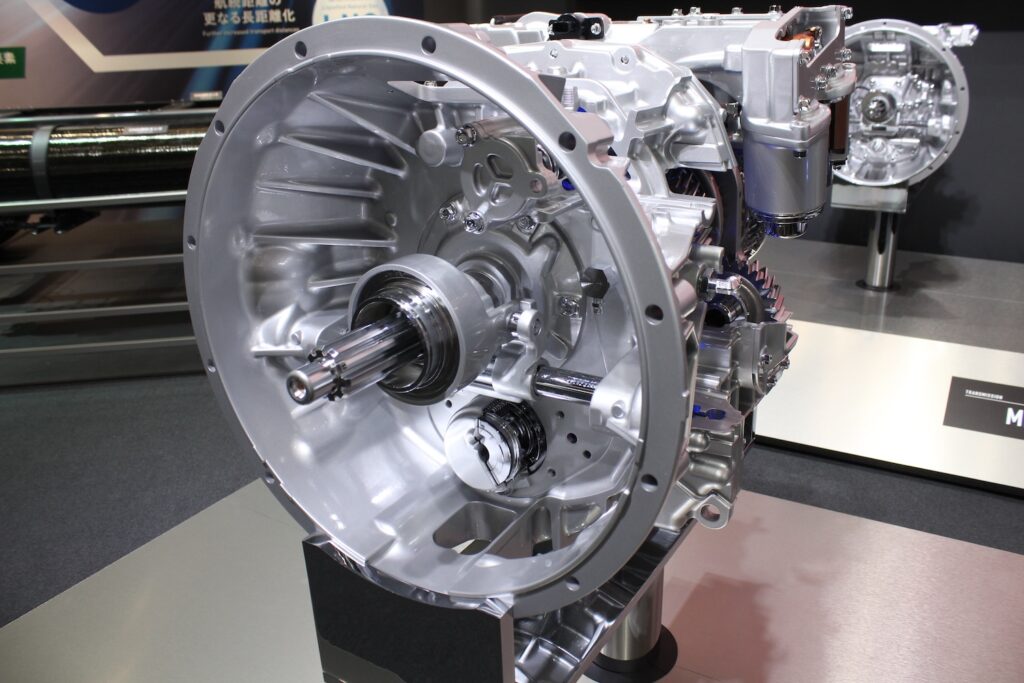